Accurate estimates are essential for setting budgets and ensuring project success. However, multiple variables can influence costs, creating discrepancies between initial projections and final expenses. In this article, we’ll explore the most common factors that affect estimates, helping you better understand the complexities and make well-informed decisions.
Project Scope
The project scope lays the groundwork for what the project will entail, defining objectives, deliverables, and tasks. This factor significantly impacts both time and resources, ultimately shaping the project cost.

Scope Complexity
Complexity is a significant driver of cost within the project scope.
- Detailed Work Breakdown: Projects with intricate tasks, such as specialized engineering or highly technical work, usually require additional resources and expertise. A comprehensive breakdown structure often calls for specialized skills and materials, increasing the budget.
- Interdependencies: Complex projects usually have tasks that rely on each other, requiring careful planning. Coordinating these interdependent tasks can lengthen timelines and boost costs due to the need for skilled personnel to manage the sequencing.
- Special Requirements: Projects with unique specifications or high-quality standards also tend to be more costly. Meeting stringent standards typically requires additional time, resources, and sometimes rework, adding to labor and material expenses.
Scope Changes
Mid-project changes to the original scope can cause significant cost increases.
- New Deliverables: Adding extra deliverables after the project has begun usually requires more resources and extended timelines, which impacts labor and materials.
- Revision Cycles: Frequent revisions can add unexpected costs. Each cycle requires more time from skilled personnel and can delay other tasks, making the project more expensive overall.
- Rework: Changes after work is completed may require parts to be redone. For example, demolishing and redoing completed sections due to changes in requirements can be costly and time-consuming.
Material and Equipment Costs
Materials and equipment are major budget components. Costs can vary based on the type, quality, and quantity needed, as well as market fluctuations.

Material Quality and Quantity
Choosing the right materials directly influences the overall project estimate.
- Premium Materials: Opting for high-quality materials, such as luxury woods or custom fixtures, can substantially increase costs. Specific finishes and custom materials often come at a premium.
- Bulk Purchasing: Ordering materials in bulk can reduce per-unit costs but also demands accurate forecasting. Over-ordering wastes resources, while under-ordering can result in delays and price changes if additional materials are needed later.
- Availability and Sourcing: Rare or imported materials often cost more and may be subject to shipping delays, adding to expenses. The sourcing method and distance also impact the final cost, as long-distance transportation incurs extra fees.
Equipment Rentals or Purchases
Certain projects require specialized equipment, which can greatly affect costs.
- Heavy Machinery: Renting or buying machinery like excavators or cranes is costly, especially if needed for extended periods. The rental duration and specific equipment needs influence this expense.
- Operator Fees: Specialized equipment requires trained operators. If operators are rented along with equipment, both rental and labor costs rise accordingly.
- Maintenance Costs: For long-term rentals, equipment may require regular maintenance, adding additional expenses for fuel, repairs, and upkeep to keep operations smooth.
Market Fluctuations
Market conditions can make material costs unpredictable, which can have a big impact on estimates.
- Demand and Supply Changes: Global market shifts, such as sudden demand spikes for materials like lumber, can inflate costs.
- Seasonal Variations: Some materials are costlier during peak seasons. For example, insulation may become more expensive in winter when demand surges.
- Transportation Costs: Fuel price changes and import taxes affect material costs. When materials are sourced from distant locations, transportation fees can significantly impact the project budget.
Labor Costs
Labor is another substantial part of project estimates, as it covers both skilled and unskilled workers required for various tasks.

Skill Level and Expertise
Highly skilled labor can drive up project costs.
- Specialized Talent: Projects requiring specific technical skills, such as certified electricians, demand higher wages, impacting the labor budget.
- Training and Certification: Complex projects may need licensed professionals, which can increase costs due to premium pay and, sometimes, additional training costs.
- Limited Talent Availability: In regions where skilled labor is scarce, higher rates may be needed to attract or retain qualified workers, especially for specialized roles.
Labor Hours and Overtime
The time required for labor also affects costs.
- Overtime Needs: Tight timelines may require overtime work, which generally incurs higher pay rates. This leads to increased labor costs.
- Shift Scheduling: For extended projects, shift rotations prevent worker fatigue but may require additional labor to cover all shifts, adding to costs.
- Task Dependencies: Waiting for previous tasks to complete before moving to the next stage can lead to downtime. If workers are paid during downtime, this also adds hidden costs to the budget.
Geographic Location
Labor costs often vary based on the project location.
- Cost of Living Variations: In high-cost areas, wage expectations are higher, especially in urban centers where labor rates are influenced by local living expenses.
- Local Market Rates: Local labor rates also vary regionally, and limited labor availability can increase costs. For instance, rural areas may require higher pay to attract skilled professionals.
- Travel and Lodging: Remote projects may incur extra costs for worker travel and lodging, especially if the project is in a rural or hard-to-reach area.
Permits and Legal Fees
Securing permits and ensuring legal compliance can also add to project costs, especially in complex projects or regulated industries.

Permit Costs
Certain permits may be mandatory depending on the nature and location of the project.
- Building Permits: Major construction projects require permits, which come with fees that vary by jurisdiction and project size.
- Environmental Permits: Projects impacting the environment may need additional permits, which incur fees for waste management approvals or environmental assessments.
- Historical or Heritage Permits: Projects involving historical sites require compliance with heritage regulations, which can add to costs due to special conditions.
Compliance Costs
Ensuring that a project meets legal and safety standards is often a costly but necessary component.
- Safety Equipment and Training: Compliance with local regulations means investing in safety equipment and possibly training sessions, both of which add to the budget.
- Documentation and Reporting: Proper compliance often involves extensive paperwork and reporting. Dedicated staff or consultants may be needed to handle these aspects.
- Penalties for Non-Compliance: Failure to comply can result in fines or project delays, both of which lead to increased expenses.
Inspection Fees
Regular inspections by authorities may also impact project estimates.
- Routine Inspections: Certain projects undergo frequent inspections, with each inspection potentially incurring a fee.
- Corrective Measures: If issues are identified during inspections, corrective actions may be needed, often requiring rework or additional resources, adding unanticipated costs.
Contingency and Risk Factors
Unexpected challenges are almost inevitable in large projects, so it’s wise to account for risks and have a contingency budget.
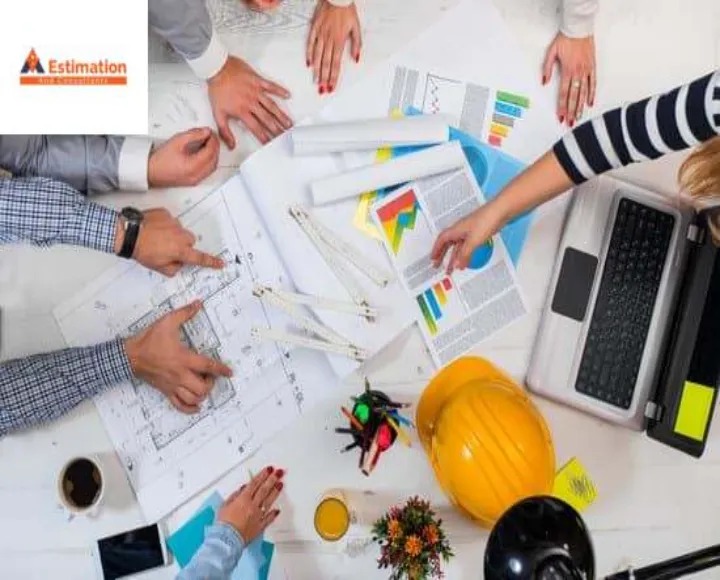
Unexpected Issues
Unforeseen problems can arise that affect the overall budget.
- Weather-Related Delays: Outdoor projects are particularly vulnerable to weather conditions, which may lead to delays and increased costs.
- Unforeseen Site Conditions: Challenges like unexpected soil types or hidden obstacles can require changes in design or materials, increasing costs.
- Supply Chain Disruptions: Interruptions in the supply chain, such as material shortages, can delay projects and require sourcing from costlier alternatives.
Contingency Budgeting
Including a contingency fund is essential to managing these risks effectively.
- Allocated Reserves: Contingency funds are set aside to cover unexpected expenses. Higher-risk projects usually require larger reserves.
- Proactive Risk Assessment: Identifying risks in advance allows for strategic planning and minimizes the financial impact of unexpected events.
Conclusion
Understanding these factors that affect estimate costs allows project planners to create more realistic budgets and anticipate potential cost variations. Recognizing the influence of project scope, material and equipment expenses, labor needs, permit and legal requirements, and risk factors leads to a comprehensive approach to estimating. Whether managing a small business project or a major initiative, considering these factors will improve cost accuracy and keep your project on track.
For expert assistance with accurate estimates and efficient cost management, contact AS Estimation & Consultants today to streamline your project’s financial planning.